
Here is an example of a typical two blade
prop mold. The mold pictured is a high temp mold capable of cures up to 350 deg.
fahrenheit. Although most resins suitable for propeller making do not have to be
cured at such high temperatures it is nice to have this high temp feature. The
idea behind this mold was to cure the blade in the mold under heat to give it
better structural properties at a higher operating temperature. By using a 250 degree
resin the blade was molded to a thinner cross section without the problem of
creep. The higher temp resins afford better wetting than room temp resins do on
average. When a resin reaches a warm state the viscosity drops and further
enhances wet out. The problem with getting the resin too warm is you loose
your working time. Sometimes it feels more like an art than science. There are
too many variables out there for the manufactures to cover every process, so it
is up to the fabricator to develop his own processes and materials. When
working with metals you don't have to worry about the alloy since it is already
created for you, but when working with composites you are creating the alloy so
to speak. If the blade was demolded before post curing you would have to
have some way of supporting it to keep it from distorting. With the tolerances
being so tight on the pitch this was out of the question. So the decision to
cure the propeller in the mold was made. The mold pictured is for a 13 inch
propeller at 4 to 3 inches of pitch. Click
Here For The Production Process Of A High Temperature Propeller And Mold
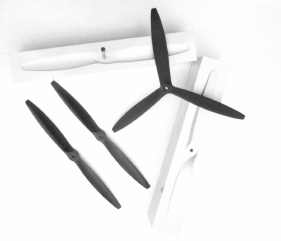
Some more propellers with a room temp mold.
The three blade has a lot of chord and was developed for a 60 size side exhaust
engine. The chord was too much and had to be reworked into a plug for another
mold. The nice thing about composite propeller molding is the advantage of
making a part and testing it, then changing it to make another mold, so the part
sort of goes through this evolution process to arrive at the elusive perfect
part, so to speak. Once a mold is made I never change the master part that made
it. This enables me to make another mold if the mold wears out or is damaged.
The part that comes from the mold is modified to make another mold.
Another example of experimentation.
Typical
three blade composite mold. It's not my intention to sell any props in the near
future but I would like to pass along this technology in the form of a video
produced by Robins View Productions in the future. I feel that the video medium
would be the best choice for conveying this information. Bob Hunt of Robins
View Productions produces high quality videos with state of the art editing
techniques. Check out his web site by clicking on the hyperlink above.